KNAUF dry floor screed: a good choice!
To level the floor for the flooring and raise the base to the desired level, perform a screed. Such a structural element is made in various ways. One such method is dry screed. This method is popular due to its simplicity and other positive characteristics. To make a reliable, durable coating, it is recommended that you choose a quality material. Dry screed from the German company Knauf is in demand. The material helps to complete the rough coating in a short time without making any effort.
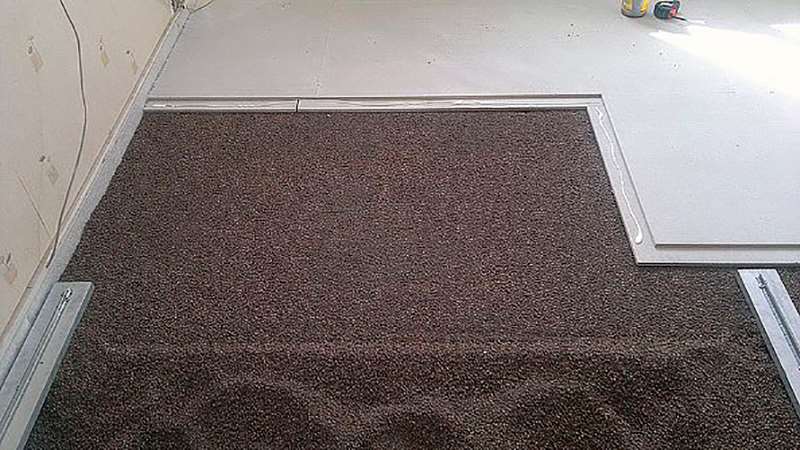
The content of the article
- What is a “dry screed”?
- Benefits of Dry Floor Screed
- Scope and need for dry screed
- We deal with the advantages and disadvantages of dry screed
- Work order
What is a “dry screed”?
Dry screed - a multilayer floor covering, which includes waterproofing material, a dry fine-grained filling and drywall sheets for leveling. The result is a solid structural element that can withstand increased loads.
As a filling under drywall use expanded clay. The fraction size in this case is less than 4 mm. This material is called expanded clay sand. The composition is poured onto a waterproofing film. The layer thickness is 3-15 cm, depending on the size of the differences. Further, the material is aligned with pre-installed beacons. Plaster sheets are laid on top. Thanks to this product, expanded clay is compacted, making a reliable foundation.
Knauf dry floor screed is a combination of expanded clay sand and plasterboard material, which completes the rough coating. The company has been producing such a product since the 50s. 20th century. During this time, the material has proven quality, reliability and durability.
Benefits of Dry Floor Screed
Dry screed has many advantages over wet laying. However, this version of the rough coating has disadvantages. Before proceeding with this type of finish, it is recommended that you familiarize yourself with the characteristics, as well as the advantages and disadvantages of the material.
Scope and need for dry screed
Knauf dry screed is performed in the following situations:
- in the presence of differences in the construction base from 4 cm;
- if you want to hide engineering communications;
- if the construction base is made of wood or has logs;
- if you need to quickly screed the floor and there is no time to wait until the wet coating dries.
Scope of a dry coupler:
- rough coating in multi-storey and private houses, as well as in commercial premises;
- for restoration of dilapidated houses;
- for buildings made of wood;
- in unheated rooms.
We deal with the advantages and disadvantages of dry screed
Dry screed has the following advantages over the wet roughing method:
- the absence of moisture in the coating prevents leakage, and also protects neighboring rooms from moisture penetration;
- the materials are sold ready-made - there is no need to knead the mortar, which reduces the time for arranging floors and helps to save on the purchase of a construction mixer or other similar tool;
- no need to wait for the mortar to solidify, so the finish coating is mounted immediately after laying drywall sheets;
- if the need arises, a dry screed is quickly dismantled without effort and using a special tool;
- rough coating is allowed to be done room by room, without fear of loss of height;
- any floor covering is suitable;
- light weight of the material - this reduces the load on the supporting base, which is important for dilapidated buildings in need of restoration.
Dry screed Knauf has these, as well as the following advantages:
- levels the surface, which facilitates the application of the finish coating;
- does not cause allergies, since the material is considered a hypoallergenic product;
- increases the thermal insulation of the room, which eliminates the need for arranging warm floors;
- makes it possible to lay thin floor coverings - linoleum and others;
- fire resistance, therefore in case of fire the fire will not spread along the screed;
- sound insulation, therefore, when walking on the floor there are no unpleasant characteristic sounds;
- ease of installation, so a beginner can equip a screed;
- You can lay the rough coating at any time of the year;
- there are no harmful chemical compounds in the composition, which indicates the environmental friendliness of the product and the safety of the use of the material;
- hides engineering communications that negatively affect the appearance of the finish;
- when laying special tools are not required.
Despite the advantages, a dry screed also has disadvantages:
- Low moisture resistance. Accidental moisture penetration into the screed, for example due to flooding, will require thorough drying of the layers by opening the floor covering or completely replacing the rough foundation. For this reason, such floors are not equipped in rooms with high humidity, as well as in poorly heated rooms.
- During the filling of expanded clay, dust rises, so it is worth using personal protective equipment when installing floors.
- Great value. The price of a dry screed, especially Knauf materials, is several times higher than the cost of funds for arranging a rough coating in a wet way.
- Screed Height For this reason, such a rough coating is not equipped in rooms with low ceilings, so as not to further reduce space.
What and how much to purchase for a dry screed device?
Since materials for arranging a dry screed are of high cost, it is necessary to accurately calculate how much money is needed per 1 m. For this, take into account such nuances:
- dimensions of the room;
- the height to which the screed is erected;
- size of materials;
- ways to place products.
In order to equip a dry screed, you need to calculate the need for the following building products:
- expanded clay;
- drywall;
- damping tape;
- PVF film for arranging waterproofing;
- lighthouses;
- self-tapping screws;
- PVC glue.
You will also need such tools:
- a drill and a screwdriver for drilling holes in drywall sheets and twisting self-tapping screws;
- drywall knife or other similar tool for cutting sheets;
- tape measure or other measuring device;
- rule for leveling expanded clay.
Video: which backfill is better to choose for a dry screed
In the video, a professional talks about which expanded clay is better for arranging a dry screed.
Calculators for calculating the required amount of materials for dry screed
A special online calculator will help you calculate the needs of products for arranging a rough coating. However, an accurate calculation can be done without a special program.
The amount of dry backfill
The calculation of expanded clay is carried out based on the volume of the product. To do this, the area of the room in which the rough coating is arranged is multiplied by the height of the screed. For example, if the area is 50 m2, and the height of the screed is 8 cm, then the calculation of the amount of material is performed according to the following formula:
50 * 0.8 = 4 m3 expanded clay.
After that, they look at the manufacturer's recommendations indicated on the package. Expanded clay from the Knauf company has an expense - 475 kg per 1 m3. Therefore, according to the data above, it will take 475 * 4 = 1900 kg. If we take into account that the material is produced in bags weighing 24 kg, then approximately 80 bags will be required for screeding the floor.
The amount of remaining consumables
Drywall calculation is also done based on the area. The size of the material from Knauf is 2.5x1.2 m or 3 m2. To find out the exact number of sheets, you need to divide the room area by the size of the material. In the above example, the formula looks like this:
50/3=17
Professionals recommend making a reserve in case of unforeseen circumstances. In this case, 19 sheets of drywall should be purchased.
In addition to drywall and expanded clay for floor screed, PVC glue and screws are required. Knauf recommends using 10 screws on 1 sheet of material. Therefore, in the above example, 190 self-tapping screws on 19 sheets will be required. It is also recommended to use 400 g of glue per 1 sheet of material. 19 sheets will require 7.6 kg of funds.
A waterproofing film is required for the entire area of the room. It is recommended to take the material with a margin for joints and overlap on the walls. In the above example, approximately 6 m2 of waterproofing material will be required.
The flow rate of the damper tape is equal to the perimeter of the room.
Work order
When arranging a dry screed, it is important to follow the work procedure. This guarantees the quality of the screed and a long operating period of the coating.
Video: floor installation using dry screed technology
The video in this article demonstrates the rules for installing Knauf dry screed.
Preparation for installation of dry screed
To lay a dry screed, the construction base is prepared as follows:
- Dismantle the old flooring.
- Check the surface for cracks and if defects are found, increase their size. Primed twice with a break for drying and fill with a solution.
- After the composition hardens, the construction base is freed from dust and dirt.
- Metal elements are dismantled, and if there is no such possibility, anti-corrosion treatment is carried out.
- In the presence of large surface differences, the protrusions knock down to make a relatively flat building base.
After that, determine the height of the screed. To perform this manipulation, a laser level is required. Since this is an expensive tool, for a single use it is advisable not to purchase the tool, but to rent it. The height is determined as follows:
- The laser level is installed in the center of the room so that the lines fall on all the walls of the rooms that are adjacent to the room.
- For marking, draw a line around the perimeter of the room.
- From the marking, the distance to the coating is measured and the upper point is calculated - this is the minimum height of the screed, which they are guided when attaching the damper tape and installing profiles.
Laying a vapor and waterproofing membrane and damper tape
The presence of steam and waterproofing is a prerequisite for dry screed. This guarantees a long operational period of coverage.As a waterproofing coating, it is recommended to use a conventional PVC film. The material is laid out on a building base with an overlap of 20 cm on each other and with an overlap on the walls in the height of the coating. The seams of the film are fixed with construction tape.
Then the material is fixed to the wall with a damper tape. It is recommended to use a product with an adhesive side. Such material is more convenient to fix on the wall. If there is no adhesive strip, then the damping tape is fixed using industrial tape. This material not only allows you to fix the film on the wall, but also increases the waterproofing of the rough coating and the building base. We recommend attaching the damping tape 2 cm above the screed.
Installation of gypsum fiber floor elements
Before installing drywall on a waterproofing coating, beacons are installed and expanded clay is poured. Do this as follows:
- Set the guides. Lighthouses are fixed on a building base with self-tapping screws. Next, the profiles are aligned with the rule.
- Expanded clay fall asleep. The material is laid from the wall opposite the door. Expanded clay fill the entire space between the profiles.
- The material is leveled on a building basis. Do this with the rule. The tool is mounted on beacons and guided. Excess expanded clay is removed.
- Profiles are dismantled. Lighthouses are taken out immediately after filling one “track” of material. The voids are filled with expanded clay. However, beacons are left on which drywall is fixed.
- After leveling expanded clay, drywall is laid. On sheets that are located near the walls, the fold is cut from the side that will adjoin the wall.
- The first sheets are mounted along the wall opposite the door. Next, the folds of the material are treated with glue and the second row of drywall is laid.
- When the floor is covered with sheets, the seams of the sheets are pulled together with screws at a distance of 30 cm from each other. After that, a thin layer of putty is applied to the joints. It is recommended to choose a material specifically designed for drywall.
- Apply a deep penetration primer. The primer is also chosen specifically for drywall.
- After that, the finishing flooring is laid.
Video: amateur installation dry screed errors and their correction
If a dry floor screed is performed by an amateur, he can make mistakes that lead to a deterioration in the appearance of the finish and shorten the life of the coating. In the video, professionals demonstrate the most common drawbacks of the screed and show how to eliminate them.
Dry screed Knauf is a high-quality and reliable material that serves without loss of performance over a long period. For this reason, the product is popular with professional craftsmen and amateurs, despite the high cost.